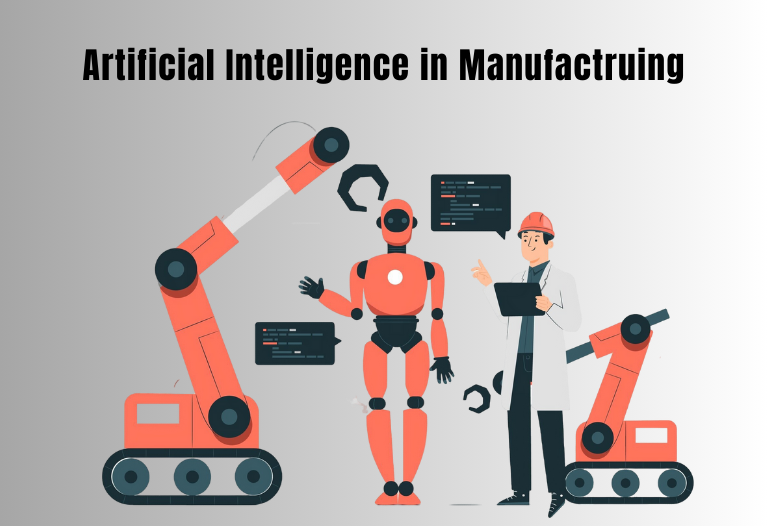
Artificial intelligence (AI) has emerged as a game-changer in the rapidly evolving manufacturing world, redefining how businesses operate. By integrating AI in manufacturing processes, you can achieve unparalleled efficiencies and position your business for long-term growth and competitiveness.
If you own a manufacturing business and are considering AI implementation, understanding its transformative potential is critical. Let’s explore 9 compelling benefits that make AI indispensable in modern manufacturing.
1. Enhanced Operational Efficiency
AI-driven systems optimize production workflows by analyzing vast datasets in real-time. For example, predictive analytics can identify potential bottlenecks in assembly lines, enabling proactive adjustments to maintain optimal throughput.
Companies like BMW and Siemens have leveraged AI to streamline operations, reducing production downtime by up to 30%.
Case Study: Predictive Maintenance at GE Aviation
GE Aviation implemented AI-powered predictive maintenance (GE Predix, their own AI platform) for its manufacturing equipment, reducing unplanned downtime by 50%. Sensors and AI algorithms monitored machine conditions, predicting failures before they occurred. This minimized disruptions and significantly saved them over $1 billion in maintenance costs.
Implementation Details:
- Sensor Integration: GE equips its machinery and jet engines with a network of sensors that continuously collect data on various parameters, including temperature, vibration, and pressure. This real-time data collection is crucial for monitoring equipment health.
- AI Algorithms: The collected data is analyzed using sophisticated AI and machine learning models capable of detecting patterns indicative of potential failures. These algorithms learn from historical data to improve their predictive accuracy over time.
- Predictive Maintenance Scheduling: By accurately forecasting equipment failures, GE can schedule maintenance activities proactively, thereby minimizing unexpected breakdowns and optimizing maintenance resources.
Outcomes:
- Reduction in Unplanned Downtime: GE’s predictive maintenance approach has led to a significant decrease in unplanned downtime, enhancing overall operational efficiency.
- Cost Savings: Proactively addressing maintenance needs has resulted in substantial cost savings by preventing major equipment failures and extending the lifespan of machinery.
- Enhanced Safety and Reliability: Continuous monitoring and early detection of potential issues have improved the safety and reliability of GE’s operations, particularly in the aviation sector where equipment performance is critical.
This case study exemplifies the transformative impact of AI-driven predictive maintenance in the manufacturing and aviation industries, highlighting how real-time data analysis and proactive maintenance strategies can lead to significant operational improvements.
2. Improved Product Quality
AI enables manufacturers to maintain consistent product quality by identifying defects early in the production cycle. Computer vision systems powered by AI can detect minute anomalies invisible to the human eye. This ensures higher standards and fewer defective products reaching customers.
For example, Tesla employs AI-driven vision systems to inspect components during vehicle assembly. This has resulted in fewer recalls and enhanced customer satisfaction, showcasing AI’s impact on maintaining quality at scale.
3. Cost Reduction
Implementing AI reduces waste, optimizes resource allocation, and lowers operational costs. Machine learning algorithms can analyze energy usage patterns and suggest efficient power consumption strategies, saving costs without compromising production goals.
Industry Insight: Nestlé reduced operational costs by integrating AI into its supply chain. By forecasting demand more accurately, the company decreased inventory carrying costs by 15%.
4. Increased Workplace Safety
AI-powered safety systems enhance worker safety by monitoring factory environments and identifying potential hazards. Robots equipped with AI can perform high-risk tasks, minimizing human exposure to dangerous conditions.
Case Studies: Collaborative Robots at FANUC
FANUC uses AI-driven collaborative robots (cobots) that can work alongside humans without safety barriers. These cobots identify hazardous situations and take corrective actions, reducing workplace accidents.
Enhancing Ergonomics at STIHL
At STIHL, a renowned manufacturer of chainsaws and handheld power equipment, implementing FANUC’s CR-35iA collaborative robot has significantly improved workplace ergonomics. In their assembly line, the cobot assists in handling heavy components, relieving workers from physically strenuous tasks. Operating at a safe speed of 250 mm/s in collaborative zones, the CR-35iA ensures seamless integration with human workers, enhancing productivity while maintaining safety standards.
Another Example Could be Cost-Effective Quality Inspection at Flex-N-Gate
They faced challenges in ensuring product quality due to traditional inspection systems’ high costs and spatial demands. They developed a flexible and cost-effective inspection process by integrating FANUC’s CR-7iA collaborative robots equipped with cameras. These cobots maneuver cameras to critical inspection points, reducing the need for multiple fixed cameras and extensive safety enclosures. This innovation lowered equipment costs and saved valuable production space, enhancing overall operational efficiency.
5. Customization and Flexibility
AI facilitates mass customization by enabling manufacturers to quickly adapt to changing consumer demands. Machine learning algorithms analyze market trends and adjust production processes to create personalized products at scale.
For instance, Adidas leveraged AI in its Speedfactory to produce custom shoes tailored to individual customer preferences. This approach not only improved customer satisfaction but also reduced production lead times.
6. Supply Chain Optimization
AI enhances supply chain efficiency by improving demand forecasting, inventory management, and logistics. Advanced algorithms analyze data from multiple sources to anticipate market shifts and adjust supply chain strategies accordingly.
You should take note of the real-world impact. One of the ecommerce giants – Amazon’s use of AI in its supply chain ensures timely delivery and optimized inventory levels. By predicting demand fluctuations, the company maintains a competitive edge in e-commerce.
Before we can discuss AI innovation, we must discuss the benefits of Integrating Agentic AI and Hyper-Personalized AI Agents in Manufacturing, which is the next big thing in AI.
The advent of agentic AI and hyper-personalized AI agents has revolutionized how manufacturing firms interact with their processes and stakeholders.
These advanced AI systems exhibit autonomy, making decisions and taking actions based on pre-defined goals without constant human supervision. Their integration into manufacturing environments can significantly enhance efficiency, precision, and adaptability.
Agentic AI: Autonomous Decision-Making
Agentic AI systems are designed to independently analyze data, assess conditions, and make operational decisions in real time. This translates to autonomous production line adjustments, optimized resource allocation, and dynamic scheduling based on changing demands in manufacturing.
For instance, an agentic AI system can detect a slowdown in a specific assembly line and reassign tasks to balance workloads across the facility. This not only prevents bottlenecks but also maximizes machine utilization and productivity.
Hyper-Personalized AI Agents: Tailored Solutions
Hyper-personalized AI agents take automation further by catering to individual preferences, needs, or conditions. In a manufacturing setting, these agents enable tailored machine configurations, customized employee training modules, and supplier communication optimized for specific client requirements.
For example, AI agents can create personalized maintenance schedules for different equipment, considering wear-and-tear patterns unique to each machine, reducing downtime, and extending lifespans.
7. Accelerated Innovation
AI empowers manufacturers to innovate faster by automating R&D processes. Generative design algorithms, for example, can explore thousands of design options, helping engineers identify the most efficient and cost-effective solutions.
You can take inspiration from Boeing’s AI-Driven Aircraft Design. They utilized AI algorithms to analyze aerodynamic performance and material properties, leading to innovative designs that enhance fuel efficiency and reduce costs.
8. Sustainability and Environmental Benefits
AI helps manufacturers reduce their environmental footprint by optimizing energy consumption and minimizing waste. Smart energy management systems powered by AI ensure efficient resource utilization.
Case Study: Schneider Electric’s Sustainability Goals
Schneider Electric integrated AI into its manufacturing plants, achieving a 25% reduction in carbon emissions. The company implemented sustainable practices by analyzing energy consumption patterns without sacrificing productivity.
Schneider Electric’s flagship project in AI-driven sustainability is its Lexington, Kentucky facility, which is designated as a Smart Factory. This plant leverages EcoStruxure™ — the company’s IoT-enabled platform — to harness the power of AI. Through this integration:
- The facility reduced its energy costs by 26%.
- Carbon emissions were significantly curtailed by aligning machine operations with optimal energy schedules.
- Real-time monitoring enabled a closed-loop system that continually improves energy efficiency.
9. Improved Decision-Making
AI provides actionable insights by analyzing complex datasets, enabling manufacturers to make informed decisions. From production schedules to market strategies, AI ensures that decision-makers have access to accurate and timely information.
For instance, Procter & Gamble uses AI to analyze consumer data and forecast demand. This data-driven approach has improved decision-making processes, improved product availability, and increased customer satisfaction.
Overcoming Challenges in AI Implementation
While the benefits of AI are immense, implementing it in manufacturing comes with challenges. These include high initial costs, data integration complexities, and workforce training requirements. However, partnering with experienced AI service providers can mitigate these hurdles, ensuring a seamless transition.
Why Choose Primotech AI/ML Services?
We specialize in tailored AI solutions for the manufacturing sector. We understand the unique challenges faced by manufacturers and offer end-to-end services, including:
- Consultation and Strategy Development: Identifying areas where AI can drive the most value.
- Custom AI Solutions: Designing and deploying AI systems tailored to specific manufacturing needs.
- Training and Support: Empowering your workforce to leverage AI effectively.
AI in manufacturing is not just a technological upgrade—it’s a strategic imperative. By harnessing the power of AI, manufacturers can achieve unprecedented efficiencies, innovate faster, and stay ahead in an increasingly competitive market.
If you’re ready to transform your manufacturing operations, reach out to us for AI solutions designed to propel your business forward.